Liquid separation from gas, air or steam flows - Kelburn Engineering
STEAM SEPARATION PRODUCTS
Kelburn Engineering Limited are a world leader in condensate from steam separation technology. Producing a complete range of steam separation equipment for the process, power and petrochemical industries. Our separators are designed to cover all steam applications.
HIGH EFFICIENCY COALESCENT CYCLONE STEAM SEPARATORS
Condensate droplets within the steam flow at both start up and during normal operation may cause the following problems within a steam system.
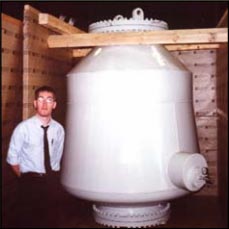
36" KSL Coalescent Cyclone Steam Separator.
- Equipment damage due to erosion and/or corrosion.
- Reduction in process efficiency due to lower heat transfer rates.
- Waterhammer.
- Thermal shock.
- Reduced heat content.
- Pipeline corrosion.
- Wire drawing effects.
The Kelburn Engineering Coalescent Cyclone Steam Separator, having been proven throughout the world, both protects equipment and prevents the problems associated with wet steam.
Liquid Droplets Coalescing Through 1st Stage Agglomerator
OPERATION
The Coalescent Cyclone Steam Separator has a two stage separation design. The first stage agglomerates the fine water particles causing them to coalesce by bringing the water droplets together, increasing in size and mass. The second stage then utilises profiled deflector blading which imparts powerful centrifugal forces to separate all the water droplets from the steam flow. The condensate exits the separator from a volute contoured drain, providing clean dry steam at outlet.
PERFORMANCE
These highly efficient, flow driven separators remove all droplets down to 10 microns in size and 80 - 90% in the range 5 - 10 microns. The separator operates with overall extraction efficiencies of more than 99.5%, giving a typical steam dryness fraction of over 0.997 at outlet from a 0.9 dry inlet steam.
The Kelburn Engineering separator generates a very low pressure drop, typically less than 1% of the system operating pressure.
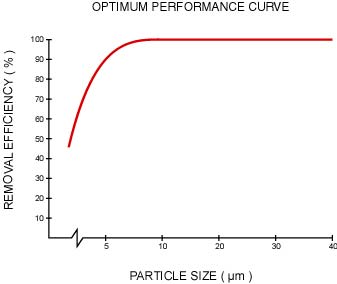
DESIGN FEATURES
- Inline inlet and outlet.
- Body of cast construction allowing manufacture in all material specifications.
- Internal contoured profile and volute drain for improved flow and separation.
- No moving parts.
- No maintenance and no spare parts requirement.
- Self clearing of separated liquids and solids.
- Low pressure drop.
- Flange and pressure ratings up to ANSI 2500 and PN 160.
- Separators specifically sized for each application, for maximum efficiency.
- Full range of separator sizes DN 10 to DN 1400 ( ¼" to 56" )
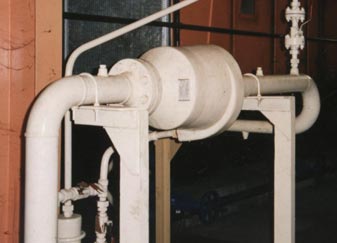
APPLICATIONS
- Steam turbine protection from blade erosion due to water particles and pipe scale.
- Pressure reducing valve, control valves and flow meter protection.
- Superheater inlet, providing dry steam to improve heat transfer efficiency.
- Boiler outlet, providing guaranteed dry steam and reducing T.D.S. levels.
- Steam main, providing guaranteed dry steam and preventing water hammer.
- Autoclaves / steam sterilizers.
- Steam injection systems on Gas Turbines.
- Flash steam lines.
- Exhaust steam lines.
- Steam turbine bleed lines.
HIGH EFFICIENCY KNOCKOUT CYCLONE STEAM SEPARATORS
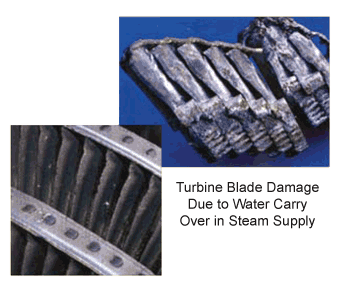
Steam plants, turbines and other equipment are always vulnerable to the ingestion of pipe scale and swarf or to the severe loadings imposed by the sudden transmission of large volumes (slugs) of water. This may result in the following problems within a steam system.
- Shock loadings due to water hammer.
- Steam turbine blading and thrust bearing damage.
- Thermal shock effects on cold fittings and ancillary equipment.
- Erosion and damage due to pipe scale and other debris.
- Overloading of condensate drainage system.
The Kelburn Engineering High Efficiency Knockout Cyclone Steam Separator has been developed to satisfy the dual separation requirement of large volumes of water and the removal of solid debris. This type of separator also provides efficient wet steam separation during normal flow conditions.
OPERATION
Slugs or streams of water, pipe scale and other debris enter the separator entrained within the steam flow and hits the coned deflector vane section (designed to withstand the large impact loadings) where the flow is split into multiple streams. The flow then enters a vortex chamber tangentially from the deflector vanes and is subjected to a powerful centrifugal action. The water and solid particles are forced to the cyclone walls and leave the unit via a large area drain. The large bore drain and pipe reservoir provide rapid liquid removal and high capacity storage during a large water carryover event, providing clean dry steam at outlet.
PERFORMANCE
These highly efficient, flow driven separators operate with extraction efficiencies of more than 99.5%, giving a typical steam dryness fraction of over 0.995 at outlet from a 0.90 dry inlet steam.
ADDITIONALLY
Separation of pipe scale, swarf and other solid debris down to 15 microns in size. Separation and dispersion of boiler prime or other water streams. The Kelburn Engineering separator generates a very low pressure drop, less than 1% of the system operating pressure.
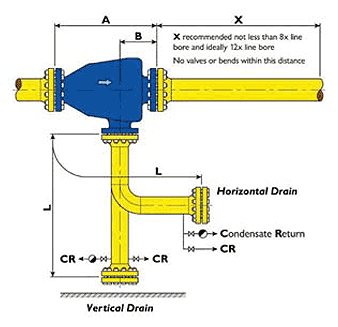
DESIGN FEATURES
- Inline inlet and outlet.
- Body of cast construction allowing manufacture in all material specifications.
- Strengthened internal vanes for absorption of shock loadings.
- Large bore drain for rapid water removal.
- No moving parts.
- No maintenance and no spare parts requirement.
- Self clearing of separated liquids and solids.
- Low pressure drop, typically less than 1% of line pressure.
- Flange and pressure ratings up to ANSI 2500 and PN 160.
- Separators specifically sized for each application, for maximum efficiency.
- Full range of separator sizes DN 100 to DN 1400 ( 4" to 56" )
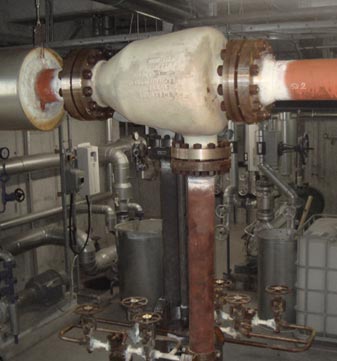
8" KSS Cyclone Steam Separator Installation
APPLICATIONS
- Steam turbine protection from blade erosion and impact damage due to water particles and high volume streams.
- Steam turbine protection from impact damage due to pipe scale, swarf and other solid debris.
- Superheater inlet protection.
- Steam main, providing guaranteed dry steam and preventing water hammer.
- Geothermal steam.